The paper seeks to improve the force developed by an AC electromagnet at maximum air-gap, using the direct optimization method by zooms, based on numerical experiments performed by finite element method (FEM) in ANSYS software. In a previous work, a 5.68% improvement in the static force characteristic of the same device was achieved and particularly, a 12.63% improvement in the force at maximum air-gap, taking into account three very influential geometrical parameters: the rate of bottom core thickness, rate of ring width and the rate of lateral core thickness. The optimization problem was subject to con-straints of maintaining the overall dimensions of the device. The research continues in this paper with the search for the optimal geometrical configuration to provide a maximum developed force in the “open” position, replacing the pa-rameter rate of ring width, having the least influence, with the parameter rate of winding thickness and adding the constraint of maintaining the cross-section of the winding. A device screening ensures that all the new three parameters are worth considering with a confidence level greater than 99%. The solution of the optimization problem brings an improvement of 25.67% of the acting force and of 7.09% of the static characteristic. The magnetic force was determined based on the principle of virtual work, available in ANSYS software. |
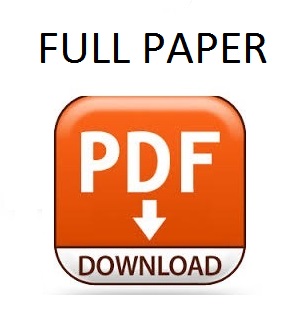 |