The opportunity of this research is to emphasize certain approaches related to the design and modeling of low and medium power permanent magnet brushless DC motors for electric vehicles, which are presently poorly treated. The challenge of any manufacturer is to develop electric machines with minimum manufacture and maintenance costs by accomplishing the performance required by the customer. One looks for mathematical models as exact as possible as tools for the design and parameter computation. As a consequence of the progress of control and power electronics, the performances of brushless DC motors have been improved. Therefore, the problems of optimal design
and optimal operating mode of such motors are currently reported by the technical literature. By exploiting the available numerical computation tools, we developed the optimized technical design of a brushless DC motor for an electric bicycle. The performed simulations emphasize the technical performances which accomplish the customer requirements as follows: manufacture cost reduction of 27.9%, total cost reduction of 9.11% and a slightly growth of the maintenance cost of 8.01%. It is advisable to do a
periodical optimal re-design, which will take into account new performant electrotechnical materials with adequate technologies, in order to decrease the fabrication cost and to increase the energy efficiency of brushless direct current motors. The optimized motor achieves the required overallsize. |
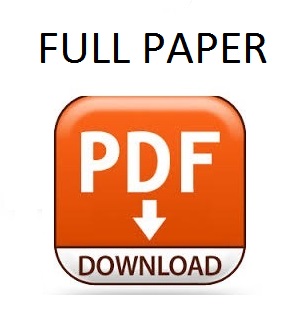 |