In this paper, the authors present an experimental analysis in order to highlight the behavior of a barrier structure model, actuated by three shape memory alloy (SMA) helical springs. The authors have developed this new barrier structure to increase the performances of conventional barriers, based on SMAs unique properties and their advantages. SMAs are advantageous for actuation because of their light weight, silent operation and flexibility. SMAs began to be increasingly present in industrial applications as well because they display high reliability and can replace the functions that make the motors or complex gears despite their simple construction. The actuator used in our model works as a linear actuator, contracting itself with great strength and speed, thus exerting the necessary force to lift the barrier arm when the SMA springs are heated by carrying an electric direct current. The designer can control the direction of actuation, the amount of force generated and the stroke of the actuator through various combinations that he can achieve with these three SMA springs. After a description of the accomplished model and of how it works, the authors present an experimental analysis of the behavior displayed by the SMA springs-based barrier structure. The experiments consisted in the determination of the SMA spring functioning time periods at constant value of the SMA spring activating electric current, and while maintaining the barrier arm stroke and weight constant. |
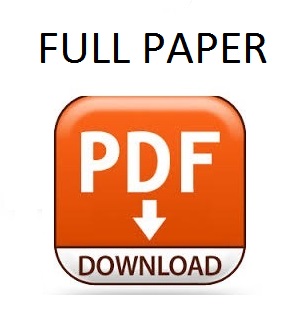 |