In this article we’ll tackle the control of electric drive with high dynamic, with rapid changes in torque and speed, where the control strategy is FOC (Field Oriented Control). In the surface mining industry, from which the electric drive application for this article is selected, the general trend is toward using asynchronous motors with shortcircuit rotor, due to the advantages of this motor both in terms of design and operation. In order to achieve the variable speed, must be used the static frequency converters. Simulations were carried out using a converter with FOC control strategy and a 45kW motor. The simulations also followed the direction from simple to complex in order to emphasize both qualitative and quantitative elements with respect to the overall dynamic behavior. Simulations were carried out both in the case where the overall structure contains an encoder for speed information, and where the sensorless approach is used the implementation of an estimator is strictly necessary. Such cases were dealt with where speed is measured directly with an encoder, compared with the case of sensorless control, where speed is estimated using a Model References Adaptive Control Estimator. Simulations were carried out in MATLAB/Simulink environment, highlighting the control structures and comparative results achieved for a drive application commonly used in surface mining industry. Following these directions a functional application was implemented and tested. |
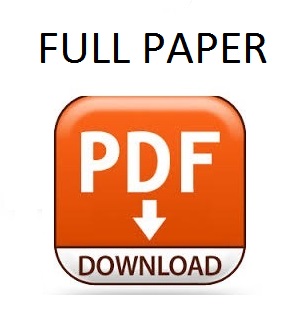 |