The trends to improve the performances of the classic instrument transformers was oriented to introducing new materials, components and methods in its design, manufacturing and operation. This paper presents the technical solutions adopted to implement the measuring system at medium voltage based on this current instrument transformer. The transformer uses a fiber optic link to send the measuring signal from the medium voltage point to the monitoring point. The structural block diagram of this transformer is presented and the operation of the main blocks is described. On the monitoring side, the measuring signal is converted from the voltage signal at the current signal which flows through a current loop for remote control and telemetry. Also, analog to digital conversion and the sending of the result of measurement at master monitoring system is possible. A simple algorithm for remote control of the operation of transformer is presented. If the transformer is integrated into a digital measurement system then it operates as a slave unit under the control of the master unit. The samples taken from the measurement signal are used for digital processing. It is analysed the possibility to realize a network of transformers using the communication bus RS 485 . Finally, the waveforms, recorded during the performed tests, are presented. |
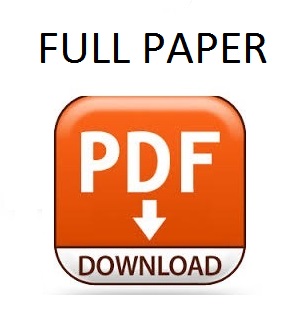 |