This paper presents the application of an exhaustive optimization method based on the design of experiments (DOE) and the finite element method (FEM), with the aim of improving the actuation force developed by a DC electromagnet. The optimization of this device has been the subject of several previous works, allowing comparisons between the optimization methods applied in terms of the obtained precision and the workload.
According to previous studies, two geometric parameters (the angle ratio of the support tip and the coil shape ratio) are very influential on the force developed at the maximum
air gap. Thus, the exhaustive optimization method took into account these two parameters for its maximization, having as constraints the maintenance of the global dimensions of the device (external radius, the height of carcass, height of the plunger with support) and of the cross-section of the winding. The optimization algorithm used the results of 2-D FEM numerical experiments carried out with the FEMM program in combination with the LUA language and is based on the response surface methodology (RSM) and analysis of variance (ANOVA). Second-order polynomial models of the objective function were calculated using full factorial designs with three levels per factor. After three iterations, a very good result was obtained, comparable to those obtained by other methods, but with a significant cost in terms of workload, the optimum obtained being a global one. |
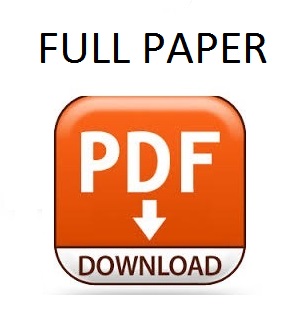 |