In this paper is proposed an optimal geometrical shape for a DC electromagnet by combining the design of experiments (DOE) and 2-D FEM. The optimization prob-lem takes into account four geometrical parameters (the coil shape ratio, the support thickness ratio, the support height ratio and the support top ratio) and consists in maximiza-tion of the acting force related to the largest air-gap, pre-serving the global dimensions of the device (the external radius, the height of carcass, the height of plunger with sup-port) and the cross-section of the winding. Before optimiza-tion, the technique of screening was applied to verify the influence of the four geometrical parameters on the acting force. The experiments were performed by numerical tool FEMM in relation to the LUA language. The acting force was computed by Maxwel Stress Tensor principle. Best in-fluence was observed for all the four parameters, especially for the support top ratio, with 99% confidence. The method by zooms without computation of models was applied to increase with 21.20% the acting force related to the air-gap of 41 mm. The cost of this improvement is the reduction of electromagnetic force for lower air-gaps which can be com-pensated by eliminating the economy resistor in this range. |
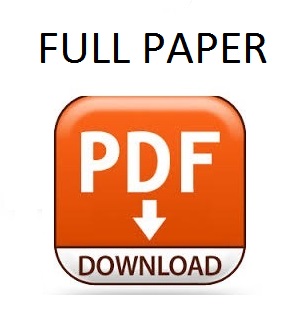 |