In this paper are detailed some results obtained within a European program in the field of avionics. The objectives of the program and the implementation team are briefly presented. A number of technical details are provided regarding the electric motor used to steer an airplane’s running gear: advantages, comparative densities between the motor used (HDD) and the competitive motors, cross-section of the used motor, winding scheme of the motor, motor scheme with partial short-circuit. The mathematical model of the motor is presented, Simulink scheme of a simulation program in case of using a voltage inverter and a series of simulations obtained with its help (MSMP supplied by a voltage inverter, transmission ratio 1000, inertia10000 Nm2 and MSMP supplied by an inverter with prescribed currents, transmission ratio 1000, inertia 10000 Nm2). The paper concludes with the conclusions obtained by conducting the research. It is mentioned that
the following notable results were obtained: decrease with 30% of the production and maintenance costs, decrease with 10% of the airship weight, carrying out a drive with a
probability to lose the functionality. |
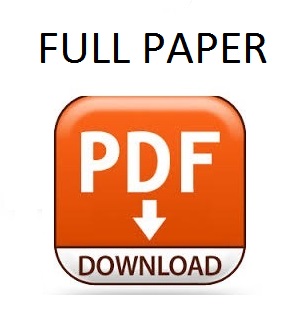 |