We have been listening for a long time to the wide functionality that industrial automation technologies can offer for improving the processes and adding security to the plants and the parts of them. However the price and an unstable market have restricted the deployment of such systems. Nowadays, companies offer too technology-dependent solutions which do not cover user demands completely. Meanwhile, papers from the literature focus on small innovations on specific parts of the industrial automation systems, which do not consider integration and deployment issues, in order to present practical designs [1]. The system presented in this work considers user requirements, including novel advances, all in an integral automation solution suitable for thermal treatments. The modular nature of the architecture allows direct adaptation to specific cases using standard technologies, and a proposal of an IP-based network for connecting the main automation module with the rest of plant. The main purpose of the entire plant is to monitor and control in real-time the temperature of the parts inserted into a resistive furnace. The software is based on m-files that contain the source code that calculates the control coefficients for the next step for ventilation and heating, it verifies the failures that could occur and creates a matrix of the coefficients, in order to make graphics. |
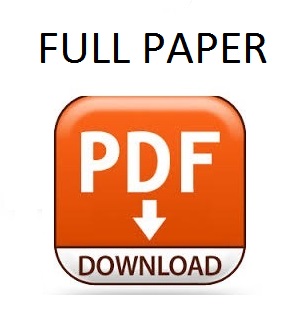 |